The pros and cons of putting a concrete countertop in your NYC apartment
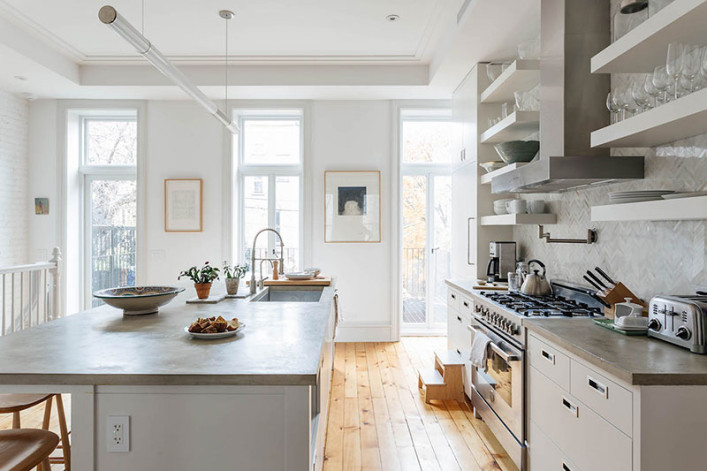
The cast-in-place concrete countertop and seamless 10-by-5-foot island with self-supporting overhang was fabricated by Oso Industries as part of a renovation by Matter Of Architecture in this Park Place brownstone.
Nick Glimenakis
Like all countertop and island surfaces, concrete has its proponents and critics—making it difficult to decide if it's the right choice for your own New York City kitchen renovation.
It certainly has its champions. “Concrete has been trending now—namely because the technology has gotten so much better,” says Jorge Fontan, founder of Fontan Architecture. He describes himself as a lifelong fan of the material. “Architects tend to like raw materials," he says.
Roy Leone, founder of Matter of Architecture, seconds that idea. He says he loves concrete as a material in general, not just for countertops but for floors and wall surfaces as well. “I love its texture and depth and also color variations.”
Then there’s its versatility and durability—certainly admirable qualities for the cornerstone component of your kitchen, which needs to tick both form and function boxes. It can be cast in any shape, tinted any color, and (contrary to popular opinion) be as smooth as you like. It is also super strong and built to last. Plus it’s all custom work, so no one will have a countertop that’s exactly like yours. (Bragging rights!)
That said, concrete takes more time to fabricate and to cure. It's also non-static and will continue to change over time, both in color but also with the inevitable dings and spots. “For our clients who are not afraid of that lived-in look, concrete is a great option. I personally like that and our clients embrace that aging and patina,” says Leone.
Still, questions and concerns arise: How will it ever fit in my apartment? Won't it just end up getting stained and cracked? Isn't it incredibly expensive?
Read on for answers and other insights from NYC architects and fabricators.
Will concrete countertops even fit in my apartment?
The answer is absolutely yes, though how yours is fabricated will depend on who is doing the work as well as your site situation—stairs and service elevators being potential obstacles.
1. The precast method: This is where the fabricator goes to the site (your apartment) and builds a template around the cabinetry and sink and other fixtures (those have to already be in place, says Fontan). Then the formwork is built and the counter is fabricated in the shop.
Some fabricators such as Trueform (which Fontan has recently worked with) will only work this way. “Everything is fabricated here, so in theory we can make one piece as long as you want it to be,” says Trueform sales director Matt Tighe.
More likely however the countertop will be installed as finished slabs, much the same way as natural stone so they can fit in service elevators or be able to navigate stairwells, though Tighe says certain clients have paid (dearly) to have one long countertop lifted with a crane and transported through a window. “We always verify the dimensions and delivery with the building, even if the client says “no problem, it will fit.”
2. The cast-in-place method: Here the fabricator will actually build the formwork around the cabinetry and pour the concrete right in the kitchen.
“The advantage of this method is that you can cast everything monolithically,” says Eric Weill, founder of Oso Industries, a custom concrete designer and fabricator. This means you can get one long piece without having any seams, what many people look to concrete to do.
Leone for one prefers this method over the other for that very reason. “I once did a job where the slabs were not really aligned all that well,” he says. (This was before he found Oso Industries, his go-to fabricator these days.)
For that reason, he and Fontan say the quality of those joints are going to depend on the quality of the craftsman, just as for other surfaces. So you need to make sure you are using people who are going to do a quality job.
With either of the above methods, you’ll usually need to plan for a three-week lead time—something you may not be willing to wait for. Or: “You could go to a stone yard and have the surface in just one day,” says Tighe.
How does concrete stack up against other surfaces?
According to the pros Brick spoke to, the advantages of concrete are numerous. Here are the top three qualities they say make it such a standout surface.
1. Style options: As a man-made material, concrete can be designed to your specifications.
“Because it is poured, you can shape it any way you like,” says Weill. This includes waterfall sides (meaning one poured piece that goes from floor to floor, such as for an island).
If you long to have a countertop with more heft, concrete is often the only way to go. Weill typically makes it two inches thick, which is slightly thicker than a normal stone top. Fontan has even installed thicknesses of three inches or more.
What usually comes up in these discussions is how heavy the concrete will be. “Just because the apron is three inches thick, the interior will only be three-quarters or one inch thick, so it’s not as heavy as you might think,” says Tighe.
Research bears this out: One square foot of one-and-a-half inch thick concrete weighs about 18 pounds, compared to 17.5 pounds for granite in the same thickness.
Of course, if you are installing a 16-foot-long, two-inch-thick countertop, that’s probably going to need extra support and reinforcement, something your architect and fabricator will be well aware of (though it never hurts to bring this up in the planning stage).
Then there’s the whole terrazzo look, which Weill says is having a design moment. “Basically you can throw aggregates in the mix, whether sand or crushed stone or even glass, and then grind and polish the cement down to expose those aggregates,” says Weill. “We’ve been doing a lot of really interesting countertops recently.”
Of course, doing this will be more costly and take more work, but “you’ll get a really nice finish,” says Fontan.
2. Color and texture variations: This might be surprising given the dull, gray, rough-hewn concrete of the past. Today’s concrete comes in an endless array of hues and a number of smooth or textured surfaces.
“Because we start with white cement and add pigments to it, it’s almost limitless in what kind of color you can do, even a bright purple countertop if you wanted to,” says Weill (who for the record has never done such a thing).
For Leone, color is often what tips the scale toward concrete, often in being able to get the exact tone of gray he is looking for, and in at least one case, a specific shade of green. “That can be difficult when using natural stone.”
Tighe says Trueform has eight standard colors and will also match the concrete to your choice from the entire 3,500 Benjamin Moore palette (for an additional cost). “And because the pigment is baked in, the concrete will be the same color throughout in case of any dings.”
And should your taste run toward a pristine white, that’s possible with concrete. “Some people seem to like that,” says Fontan.
As for texture, it runs the whole gamut, from super slick and ultra-smooth to more of a “rustic, old-school style with lots of little holes,” says Tighe.
3. Aging and patina: Concrete is not going to look the same in five years as it does the day it is installed, and this is what many fans point to as its ultimate charm. (More on this follows.)
Is concrete really prone to stains and spots?
Weill suggests thinking of concrete like marble or one of the softer stones. That means always clean up any spills right away (with a wet rag, never use chemicals) and by all means don’t use it as a cutting board or put hot pans on it.
As a porous material, concrete (like granite) needs to be sealed to protect it from stains and bacterial growth (ew), which is something your fabricator will do at the outset.
How you choose to seal is for Weill a matter of aesthetics. A “natural finish” or penetrating sealant will patina over time and get that aged look that a lot of people like, he says. (Tighe has gone so far as to leave the edges unsealed but never the top.)
On the other hand, he advises using a clear (urethane) coating if you are concerned about stains and marks and want the concrete to stay pristine.
Tighe will agree to leave only the edges (but never the top) unsealed if you want a more rustic appearance.
The recommendation is for concrete to be resealed every three to five years. “I’ve done counters for 15 years and only 5 percent of clients call me back to reseal it,” says Weill. After all, it’s not that you are going to damage the concrete itself by not resealing but rather letting the age and patina take over.
Leone takes a more proactive approach by resealing every month for the first few months, then every six months for the first two years or so, though he too is a fan of the lived-in look. “Concrete will by nature change color, and that’s a big part of its appeal.”
You can buy a “quick and easy DIY kit for about $75 from Trueform or have someone come and buff out the inevitable chips and scratches “for a minimal cost.”
If all the above gives you pause, consider quartz, which is not porous and is also sustainable. “I have been seeing people using Ceasarstone more often now for environmental purposes,” says Leone.
Doesn’t concrete always end up cracking?
Tighe explains the cement that’s used to make sidewalks and cinder blocks breaks more easily than what’s used in making countertops, which is glass fiber reinforced concrete (GFRC). “It has these little glass shards mixed in to give it more tensile strength and to make it lighter,” he says.
Fontan likes how GFRC is allows you to achieve the nice, smooth surface that seems to be more popular now.
Even when you’re not using this type of concrete, fabricators will rely on rebar or welder wire fabric for reinforcement “so the concrete can better resist any stress that might otherwise cause it to bend,” says Leone.
But make no mistake: With concrete, you will always end up with little fissures over the years, but those are not going to expand into true cracks or cause the concrete to break. Chalk those up to aging. “People actually like how those contribute to the patina,” says Tighe.
Aren’t concrete countertops incredibly expensive?
It’s important to put this question in perspective.
"Concrete countertops are all custom made and therefore are for people on a custom-made budget,” says Fontan, who finds that people generally and incredibly underestimate the cost of anything made from concrete (and end up splurging on this one component while keeping the rest of the kitchen more affordable).
Comparison also helps, and concrete tends to be in line with higher-priced marble and granite and even quartz.
Tighe says to estimate anywhere from $110 to $150 per square foot inclusive of both onsite template and installation. (He also offers a 20 percent discount to architects and designers in case you are considering dealing with the firm directly.) Given the average countertop is 40 square feet, that puts the cost upwards of $4,400.
If you desire the look of concrete but not the price tag, Fontan suggests exploring faux surfaces such as porcelain tile, though he cautions that some manufacturers do a better job than others at emulating the look of concrete. (Porcelanosa and Florim are two favorites.)
Besides having a lower price point, these surfaces are more predictable. “With porcelain for example you can put it there and forget about it,” says Fontan. “How much porcelain will change over time is miniscule compared to concrete.”
It’s entirely up to you whether that’s a good thing or not.
You Might Also Like