You can buy a 3D printed house in NY. Is this the future of home building?
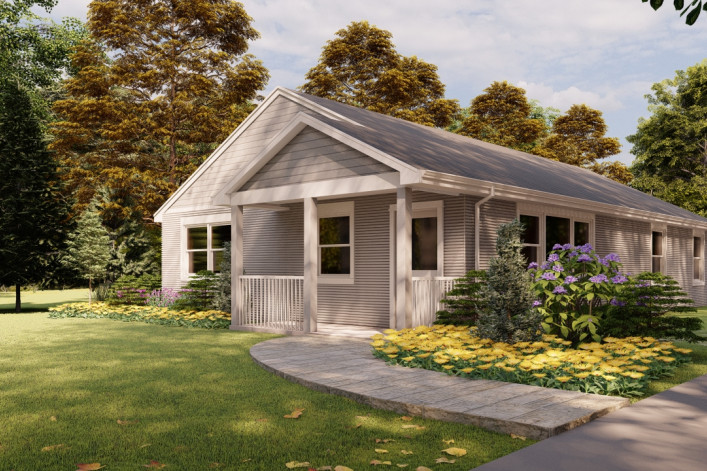
This 1,400-square-foot, three-bedroom ranch will be 3D printed in Riverhead, NY. It is listed on Zillow for $299,000.
Rendering by H2M Architects + Engineers
You may be familiar with 3D printing as a means for creating things like prosthetics, cameras, and even food. The process can be used to construct houses too—and in what feels like a game-changing development, the very first 3D printed home has been listed for sale on Long Island—even before ground has been broken.
The 1,400-square-foot house, to be created by 3D printer manufacturer SQ4D, will feature three bedrooms, two baths, and a two-and-a-half-car garage. It will be built on a quarter-acre in Riverhead, NY, and is listed at $299,000 on Zillow—far lower than the $550,000 median sales price for houses in that part of Suffolk County, according to the Elliman Report.
So is this the way of the future? Could 3D houses become the norm? Yes, according to the folks at SQ4D, who say that additive manufacturing—the technical term for the process of adding layer-upon-layer of material—offers affordability, durability, and endless customization.
"There is a huge global demand for affordable housing along with a movement toward sustainable construction," says Kirk Andersen, SQ4D's director of operations. "We wanted to be under the comps in the area and we can be with how we build. It's as simple as that."
Stephen King, associate broker at Realty Connect USA, says he is getting lots of inquiries for the house from a range of buyers, including first timers and retired empty nesters.
"When you have a $300,000 new construction on Long Island, it seems to check every box, and then there's the added draw of it being 3D printed," he says.
According to Andersen, the company's XXL printer is as much as three times faster—taking mere days rather than months to lay the foundation—and far cheaper than traditional construction methods, thanks also to its proprietary concrete mix.
How are 3D printed homes built?
The technology for 3D printing a home is essentially the same as for other 3D printed items, only on a (much) larger scale.
In fact, SQ4D started as a manufacturer of 3D desktop and custom printers but in 2017 began focusing entirely on home construction, eventually building one of the largest 3D printers in the world with on-site portability.
Andersen says they can set up their patent-pending Autonomous Robotic Construction System (ARCS, aka the printer) at a build site in six to eight hours. The machine then extrudes concrete through a nozzle, layer by layer, to create the foundation as well as the interior and exterior walls and even the utility conduits (watch it in action on the company's website). This represents about 40 percent of the total work on a house.
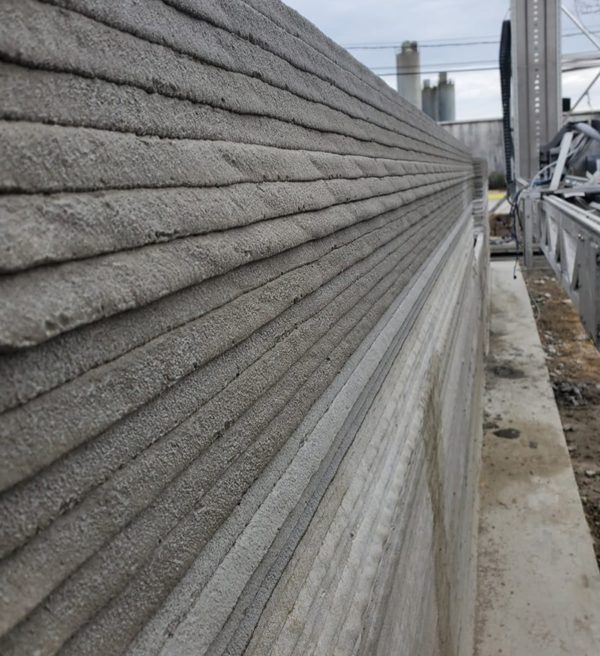
Fascinatingly, the robot has no idea of the shape or look of the house, it's just being told to go to specific spots by following the floorplan. For techno-nerds, here's how that works: The CAD file with the design is run through a "slicer" that breaks the model up into layers and then outputs those in a G code, which is the instructions on the coordinate plane as to where the machine should go. "There's definitely some secret sauce in that software that allows us to do that," Andersen says.
All the rest, meaning windows, doors, roof, and all fixtures and fittings, are handled in the traditional way, though Kevin Paul, deputy discipline director of architecture and the point person on the project for H2M Architects + Engineers (who helped ensure the design was code compliant) says the logical next step in the technology is for those elements to also be 3D printed.
Why are 3D printed homes less expensive to build?
Generally speaking, the 3D printer-slash-robot does the bulk of the "hands-on" work, replacing a traditional construction crew and consolidating the labor-intensive tasks.
For example, the SQ4D method requires only three on-site workers for the entire print. So having a robot take instructional code and accurately extrude concrete significantly reduces the costs and risk of error. It is also a safer work environment, with reduced risk of on-the-job accidents (and no need for worker's comp for the robot).
Most of all it drastically cuts down on the build time and the labor costs that would normally accrue.
Case in point: It took only 48 hours of print time over a period of six to eight days for SQ4D to construct the 3D part of its proof-of-concept house—the world's largest permitted 3D printed home (at 1,900 square feet), in Calverton, NY. So basically that initial build time is one week rather than the usual six to eight weeks. And then the rest of the house was completed within 30 to 40 days.
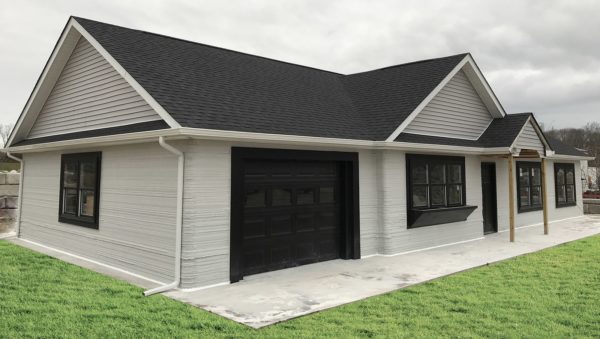
Andersen expects the print time for the listed house to be even shorter.
Putting this in perspective, King says local comps are closer to $450,000 and that it would cost a contractor over $500,000 just to build a new house on Long Island.
Andersen says some non-New York buyers don't think the price of the Riverhead house is all that affordable. But he says half of the price is to cover the cost of the land, which doesn't come cheaply on Long Island. That means in other areas where land is cheaper, the price of the house will be lower too.
What are the pros and cons of concrete houses?
According to Andersen, concrete is cheap (the materials for the demo print above totaled $6,000), abundant, and strong; SQ4D's mix has a super-high tensile strength, above and beyond what's normally used as a building material.
"Concrete is not the easiest thing to 3D print but our method of extruding it through a nozzle allows us to output a large volume of it quickly and it will hold its shape enough to be stacked," he says.
On a practical level, using concrete for the exterior walls eliminates the need for painting or siding, with minimal upkeep. Same for the interior, though buyers have the option of adding stucco or drywall. And concrete has long been a go-to material for the footing and foundation.
Andersen acknowledges that concrete has a rather large carbon footprint and that there is a global movement toward being carbon neutral. For that reason he foresees one day using a hybrid mix of recyclable materials that would have the same strength but be better for the environment.
However, since SQ4D's construction essentially involves setting up a concrete "plant" right on the job site, rather than trucking in materials from a giant factory, the process eliminates much of what contributes to the carbon load.
And in terms of electricity usage, the printer-robot runs on what is equivalent to using a hairdryer.
What are the challenges in getting 3D printed homes permitted?
New York State is known for having some of the most stringent building codes in the country—and each town has its own department to contend with.
"Any town would have difficulties with technologies that are not recognized in the building code and would therefore require the design professional to offer proof that it would be code compliant and meet all the town's concerns around life, safety, and health issues," Paul says.
So when Andersen was scouting the locale of SQ4D's second print, he and King put out calls to lots of municipalities in the area. "Riverhead was amazingly open and accepting and saw it was the future," King says.
Not that it was a done deal. As Andersen says, "it took a long year of Covid-19 and legwork and red tape but we've got the permit in hand, the building plans are approved, we own the land outright, and we'll be breaking ground in the next two months, whenever the weather breaks."
The demo house proved especially instrumental. "There's a big difference in seeing and touching and experiencing the technology and having a conceptual idea on paper," Paul says.
Going forward, having two prints under its belt may be persuasive in convincing other municipalities to accept SQ4D plans—and even paving the way for a more general acceptance of 3D printed homes.
Are these homes customizable?
The easy answer is yes. SQ4D's machine can, for example, 3D print a round wall as cheaply as a straight wall, which is not the case in traditional construction.
"You are only limited by the constraints of the technology and at this point there aren't many," Paul says.
That said, SQ4D's machine is only set up to build single-story structures, though taller 3D prints have been built in other parts of the world (and likely where there is no building code or oversight).
For its first for-sale print, SQ4D wanted to stick with the ever-popular ranch, by far the most common type of house on Long Island, to show what could be done with a familiar type of housing and make comparing prices easier. Plus King says there is always a tremendous demand for ranch-style homes.

Still, Andersen says they can create custom, high-end houses.
And Paul explains, "The technology allows you to push this beyond how you typically construct the home, so why not design in a way that actually accentuates the fact that we aren't using two-by-fours or lumber in the walls?"
Soon this might very well be another option for second-home owners who are looking to build (cheaply or not) on raw land.
How does it stack up to modular housing?
Andersen is a fan of modular construction (such as Boxabl) and does not see those companies as direct competition but rather as trying to accomplish the same thing—to put people in houses without having to break the bank.
"There are cost-savings and quality controls they see that we don't and vice versa," he says. Namely, SQ4D builds everything on site and so there's no need for a factory or transportation, whereas modular homes are built in a climate-controlled facility and then the components are delivered to the job site.
He sees 3D printing as being particularly ideal for large developments of land, where he could set up one or multiple machines to print one house after another. "There is efficiency of scale in that situation."
Other advantages of 3D printing over modular include greater customization and superior build quality, with concrete being stronger and more stable than the standard-grade compressed boards and sawdust and glue. (Not that all such modular companies rely on those materials.)
Are there any competitors?
Lots of companies around the world are building homes with 3D technology, but the playing field is limited within the U.S.
According to Andersen, there are a couple big players in the industry with different machines, processes, and concrete mixes, each carving out its own niche.
Austin-based ICON is one such company. "I love their machine design and their global mission to house the homeless," he says.
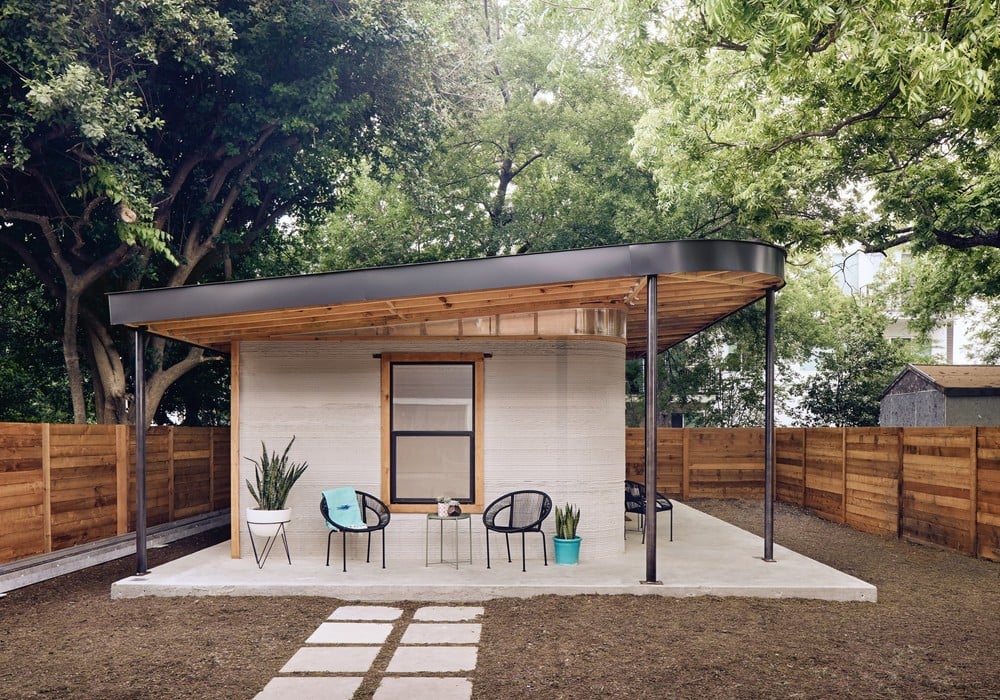
He sees more companies entering the market now that universities are teaching courses in how to apply additive manufacturing to the construction industry.
"At the end of the day we are all trying to have robots and the technology to program them replace antiquated methods," he says.
You Might Also Like