Soundproofing floors: A brownstoner's step-by-step guide
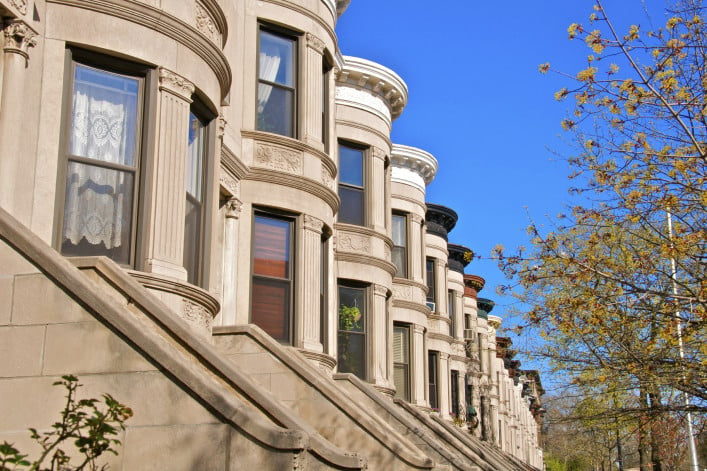
Longtime New Yorkers Angela Tiffin and Andrew Nichols bought their first brownstone in South Park Slope in May 2012, and have spent two years renovating—first, their own duplex apartment and in recent months, a third-floor rental unit—much of it with their own hands. You can read more about the project at their blog, Brownstone Cyclone.
Apartment living in NYC accustoms you to dealing with noisy neighbors, and before moving into our own brownstone in South Park Slope two years ago, we’d lived with neighbors above and below us for a decade.
Still, we decided to keep a rental unit on the top floor of our three-story, two-family house and live on the first and second floor—with the full knowledge that we’d have to put up with some noise. Until one day mid-construction we visited the house and heard some of the workers walking on the bare pine floors and imagined our future tenant with friends over at 2 am. It was time to investigate soundproofing.
After much research, we discovered that there are two types of sounds to deaden: one, the transfer of vibrations in the building framing caused by impacts on the floor (like walking), and second, noise generated by talking, music or appliances.
When people walk around, each footstep causes vibrations that travel through the floor joists and then vibrate the drywall in the ceiling. One option for reducing this is to use a drop ceiling, a second ceiling that's hung from little springs, which absorb the vibrations that would otherwise travel through the joists. We quickly vetoed this idea, since it would have meant sacrificing a few inches of our 9.5-foot ceilings and losing the crown moldings and tin ceiling on the parlor floor.
That left one route: to work from above and add a layer of soundproofing to the floor of the rental apartment.
WHAT YOU'LL NEED:
- 2 x 8 stock lumber
- ¾ BC plywood
- sound insulation
- subfloor construction adhesive
- coarse thread wood screws
- sound dampening underlayment
- finish floating flooring system
Nearly all of the supplies we used can be purchased from your favorite big box retailer. The amounts will depend on the square footage of the floor, and you’ll need about one bag of insulation, one eight-foot 2x8, and one tube of construction adhesive per sheet of 4 by 8-foot plywood. We recommend getting the underlayment and flooring from a flooring supplier. They’ll have a much better selection than the big box.
WHAT YOU'LL SPEND
$1,700 for the supplies, plus 10 to 15 weekends in sweat equity and a cranky wife
WHAT TO DO:
First, we had to pull up the 120-year-old baseboard molding, door and window casing, and the pine floor planks with a three-foot pry-bar, hammer and circular saw. This is very noisy: each time you hammer the pry-bar between the old floor and floor joist the sound echoes throughout the house. To make matters more difficult, I did this project without removing any of the existing walls. [Ed's note: Andrew takes over the project from here.] This meant carefully removing the flooring planks from under each wall in preparation for the new subfloor. To make it easier to walk around and to avoid accidently stepping through the exposed ceiling, I only pulled up about 10 to 20 feet of flooring at a time.
After removing the flooring, I cleaned the soot, plaster, and other dubious debris that had accumulated underneath with a Shop-Vac, but you technically don’t have to do this.
Next, I installed the bridges—the 2 x 8 stock cut to size, screwed in with 4-inch screws—between each joist to give them more strength and rigidity to avoid vibrating. I installed these about four feet apart running in straight lines the length of the building perpendicular to the floor joists. These should line up with the seams between each sheet of plywood.
With the bridges in place, I laid down the sound insulation, which doesn’t do much for the vibrations but does dampen noise like music or talking (plus, it’s not hard to install). A number of products are on the market for this, but I chose Roxul Safe ‘n’ Sound because it was available at my local big box hardware store, and I could buy a few bags at a time—that was all that could fit in our car.
Using an old bread knife, I cut the insulation into strips about half an inch wider than the joists and squeezed them in. You want them to fit snugly so that sound doesn’t come through the gaps.
If you’re looking to soundproof a shared wall between your apartment and a neighbor’s, this is also the stuff to use, along with sound-dampening Sheetrock.
To cover the insulation, I built a subfloor from sheets of ¾-inch BC-grade plywood, which I glued to the joists with construction adhesive and then screwed in with 2.5-inch screws. This is more time-consuming and difficult than nailing them in, but if the nails come loose the floors will squeak when people walk on them—exactly what we wanted to avoid.
Luckily, the old pine plank flooring was about an eighth inch thicker than the plywood, so I could slide the plywood underneath the existing walls fairly easily. I shimmed these gaps with some scrap wood and then screwed everything together.
Between every finished floor and subfloor, there’s a pad or vapor barrier designed to absorb vibrations. Some are as thin as paper, while others are thicker rubber or foam-like pads. We chose a relatively inexpensive product that was 80 mm thick.
Now for the finished flooring itself. This being a rental apartment, we went with a high quality durable laminate floor from QuickStep. Bonus: it’s a floating system, so the pieces don’t get nailed into the floor, which also helps with sound because vibrations can travel through nails, and nails can squeak if they get loose. We were nervous about it looking good so we hired a professional to lay down the pad and floors, which two guys finished in a day for $825.
After everything was installed, we did a test. On the plus side, the washer/dryer (which we currently have installed in the rental unit) was barely audible; likewise, anyone walking around in sneakers. We could definitely hear someone in heels, however. In the end, this was a pretty big project for us—months of work—but so far it seems to have been worth it. Of course, the ultimate test will be that night when our future tenant throws a rager and we sleep through the night.
Related:
NYC Renovation Qs: How can I soundproof my apartment?
New Yorkers' biggest home improvement delusions Renovate without conflict: why notifying your neighbors helps, plus 3 sample letters that worked
3 things we learned from a walking tour of Bed-Stuy brownstones